ОХРАНА ТРУДА, ТЕХНИКА БЕЗОПАСНОСТИ И ПРОТИВОПОЖАРНЫЕ Для бетонных и железобетонныхконструкций, на изготовление которых.
Окна, оконные блоки, остекление · Акции компаний. следующих решений по охране труда. определение средств механизации для приготовления, транспортирования, подачи и укладки бетона;. защитные очки) согласно инструкции завода-изготовителя применяемого состава.

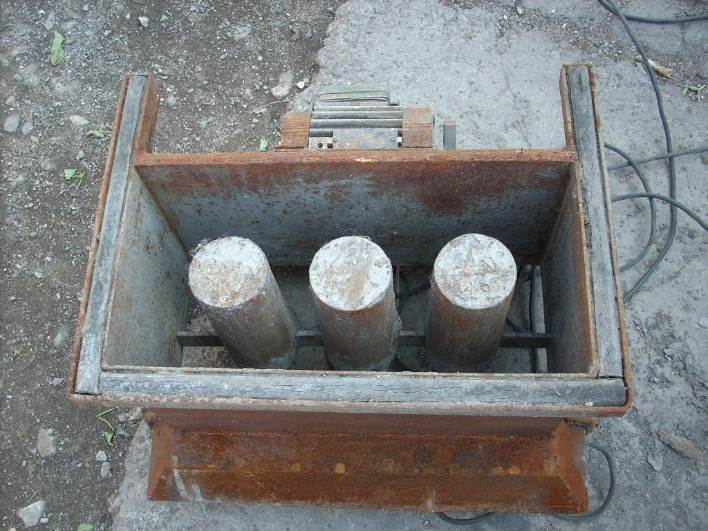
Бетонные и железобетонные работы. Инструкция по охране труда при выполнении работ. лифтов и на лестничные клетки; при установке панелей и блоков по фиксаторам и в других случаях. креплений стенок ко тлованов или траншей следует применять крепления, изготовлен -.

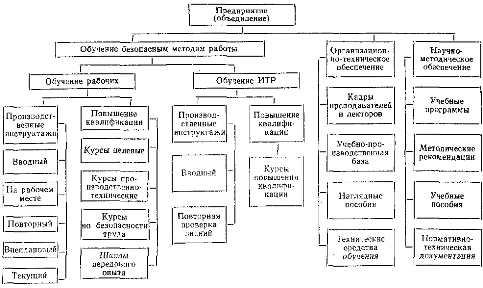
ИНСТРУКЦИЯ ПО ИЗГОТОВЛЕНИЮ ИЗДЕЛИЙ ИЗ ЯЧЕИСТОГО БЕТОНА СН 277-80 Утверждена постановлением Государственного комитета СССР по делам строительства 7 февраля 1980 г. № 9 Москва Стройиздат 1981 Содержит указания поизготовлению ячеистых бетонов и изделий из них. Приведены требования кматериалам, защите арматуры и закладных деталей от коррозии; подбор составаячеистобетонной смеси и ее приготовление; формование изделий и ихтепловлажностная обработка; укрупнительная сборка составных панелей; отделкастеновых изделий и составных панелей, контроль качества изделий и правила ихприемки, а также хранение и транспортирование изделий. Разработана НИИЖБом ГосстрояСССР с участием БВ НИИЖБ и институтов: ВНИИСтром, ВНИИЖелезобетона,НИПИСиликатобетона Минстройматериалов СССР, УралпромстройНИИпроекта ГосстрояСССР. В Инструкции использованыматериалы МИСИ им. Куйбышева, Воронежского ИСИ, Горьковатого ИСИ,УралНИИстройпроект, НИИ по строительству Госстроя ЭССР. Для инженерно-техническихработников производственных проектных организаций. Табл. 19, ил. 2. Редакторы -инж. С. М. Гунько (Госстрой СССР), канд. техн. наук А. Т. Баранов, архит. Т. В.Косточкина (НИИЖБ). 1. ОБЩИЕ ПОЛОЖЕНИЯ 2. МАТЕРИАЛЫ ДЛЯ ИЗГОТОВЛЕНИЯ ИЗДЕЛИЙ 3. ЗАЩИТА АРМАТУРЫ ОТ КОРРОЗИИ 4. ПОДБОР СОСТАВА ЯЧЕИСТОБЕТОННОЙ СМЕСИ 5. ПРИГОТОВЛЕНИЕ ЯЧЕИСТОБЕТОННОЙ СМЕСИ 6. ФОРМОВАНИЕ ИЗДЕЛИЙ 7. ТЕПЛОВЛАЖНОСТНАЯ ОБРАБОТКА РАСПАЛУБКА ИЗДЕЛИЙ 8. УКРУПНИТЕЛЬНАЯ СБОРКА СОСТАВНЫХ ПАНЕЛЕЙ 9. ОТДЕЛКА СТЕНОВЫХ ИЗДЕЛИЙ И СОСТАВНЫХ ПАНЕЛЕЙ 10. КОНТРОЛЬ КАЧЕСТВА ИЗДЕЛИЙ И ПРАВИЛА ИХ ПРИЕМКИ 11. ХРАНЕНИЕ И ТРАНСПОРТИРОВАНИЕ ИЗДЕЛИЙ ПРИЛОЖЕНИЕ 1 СОСТАВЫ, ПРИГОТОВЛЕНИЕ АНТИКОРРОЗИОННЫХ МАСТИК И НАНЕСЕНИЕ ПОКРЫТИЙ НА АРМАТУРУ ПРИЛОЖЕНИЕ 2 ОПРЕДЕЛЕНИЕ ПЛАСТИЧЕСКОЙ ПРОЧНОСТИ ЯЧЕИСТОГО БЕТОНА-СЫРЦА ПРИЛОЖЕНИЕ 3 СОСТАВЫ КРАСОК И ИХ ПРИГОТОВЛЕНИЕ ПРИЛОЖЕНИЕ 4 ОПРЕДЕЛЕНИЕ «ПЕРЕЖОГА» В ИЗВЕСТИ ПРИЛОЖЕНИЕ 5 ОПРЕДЕЛЕНИЕ УДЕЛЬНОЙ ПОВЕРХНОСТИ ПЕСКА В ТОНКОМОЛОТЫХ СМЕСЯХ С ИЗВЕСТЬЮ И ИЗВЕСТНЯКОМ ПРИЛОЖЕНИЕ 6 ОПРЕДЕЛЕНИЕ АКТИВНОГО АЛЮМИНИЯ ПРИЛОЖЕНИЕ 7 ОПРЕДЕЛЕНИЕ ПЛОТНОСТИ ПЕСЧАНОГО ШЛАМА ПРИЛОЖЕНИЕ 8 СТАТИСТИЧЕСКАЯ ОБРАБОТКА РЕЗУЛЬТАТОВ ТЕХНОЛОГИЧЕСКОГО КОНТРОЛЯ 1. ОБЩИЕ ПОЛОЖЕНИЯ 1.1.Настоящая Инструкция предназначена для руководства при изготовлении в заводскихусловиях армированных и неармированных изделий и конструкций (именуемых вдальнейшем - изделие) из ячеистого бетона всех разновидностей. 1.2.Изделия должны удовлетворять требованиям соответствующих стандартов и рабочихчертежей. Испытание ячеистого бетона должно производиться по ГОСТ 12852.0-77,ГОСТ 12852.1-77, ГОСТ10180-79, ГОСТ 12852.3-77-12852.6-77. 1.3.Изготовление изделий должно производиться по утвержденным в установленномпорядке технологическим картам, составленным применительно к условиямконкретного производства, сырья и вида изделий. 1.4.При изготовлении изделий следует соблюдать правила техники безопасности ипроизводственной санитарии на предприятиях ячеистого бетона, а также правилапротивопожарной техники. 2. МАТЕРИАЛЫ ДЛЯ ИЗГОТОВЛЕНИЯ ИЗДЕЛИЙ 2.1.В качестве вяжущих для приготовления ячеистого бетона следует применять: а) портландцемент, шлакопортландцементмарки М400 с содержанием трехкальциевого силиката не менее 50 % итрехкальциевого алюмината не более 6 %. Начало схватывания должно наступать непозднее 2 ч, а конец схватывания - не позднее 4 ч после затворения. Удельнаяповерхность цемента должна быть 2500-3000 см2/г дляконструктивно-теплоизоляционного и 3000-4000 см2/г длятеплоизоляционного ячеистого бетона. По остальным свойствам цемент долженудовлетворять требованиям ГОСТ 10178-76.Не допускается применение цемента с добавкой трепела, глиежа, трассов, глинита,опоки, пепла; б)известь-кипелку кальциевую не ниже 3-го сорта, удовлетворяющую требованиям ГОСТ 9179-77,а также дополнительным требованиям: содержание активных СаО+МgОдолжно быть не менее 70 %, «пережога» - не более 2 %, скорость гашения 5- 15мин. Тонкость помола извести должна быть с удельной поверхностью 5500-6000 см2/г,определенная по прибору ИСХ; в) цементно-известковое(известково-цементное) на основе цемента, удовлетворяющего требованиям п. 2.1аи извести - п. 2.1б. Соотношение между цементом и известью устанавливаютэкспериментально, исходя из соотношения, приведенного в п. 4.2 настоящей Инструкции; г) известково-белитовое ссодержанием свободной СаО - 35-45 % и двухкальциевого силиката - не менее 30 %.Удельная поверхность должна быть 4000-5000 см2/г. Время гидратациивяжущего должно быть 8-20 мин; д) шлак доменныйгранулированный совместно с активизаторами твердения или в составе смешанноговяжущего. Шлак должен удовлетворять требованиям ГОСТ3476-74, а также дополнительно не содержать закиси марганца более 1,5 %,сульфидной серы более 0,1 %; модуль активности для основного и нейтральногошлака должен быть не менее 0,4 и модуль основности не менее 0,9. Для помолапригоден гранулированный шлак, не содержащий плотных камневидных кусков ипосторонних примесей. Влажность при поступлении на склад не должна превышать 15%. Удельная поверхность смешанного вяжущего на основе извести и шлака должнабыть не менее 5000 см2/г; с) шлакощелочное, содержащеемолотый гранулированный шлак, отвечающий требованиям п. 2.1д и едкую щелочь,удовлетворяющую ГОСТ 2263-71*.Допускается взамен едкой щелочи применять щелочной плав. Количество едкойщелочи (Nа2О или К2О) или щелочногоплава в шлакощелочном вяжущем устанавливают путем подбора состава; ж) высокоосновное зольное(от сжигания горючего сланца, каменного и бурого угля) с содержанием СаО неменее 30 % (в том числе свободной СаО 15-25 %), SiO2 - 20-30 %, SO3 -не более 6 % и суммарного количества К2О+Na2О - не более 3 %. Удельнаяповерхность должна бить 3000-3500 см2/г. 2.2.В зависимости от вида исходного сырья состав вяжущих для приготовленияячеистого бетона следует назначать по табл.1. 2.3.В качестве кремнеземистого компонента для приготовления ячеистого бетонаследует применять: а) кварцевый песок,удовлетворяющий требованиям ГОСТ 8736-77, ссодержанием кварца не менее 85 %, слюды не более 0,5 %, илистых и глинистыхпримесей не более 3 % и не более 1 % глинистых примесей типа монтмориллонита.Допускается применение полевошпатового песка с содержанием кварца не менее 60%; б) тонкодисперсные вторичныепродукты обогащения руд, содержащие SiO2 не менее 60 %, железистыхминералов не более 20 %, сернистых соединений в пересчете на SO3 не более 2 %, едкой щелочив пересчете на Na2O не более 2 %, пылевидных,глинистых частиц не более 3 %, слюды не более 0,5 %; в) удельная поверхность,см2/г, молотого песка и вторичных продуктов обогащения руд в шламедля ячеистого бетона должна быть: 1500-2000 для объемной массы 800 кг/м3 2000-2300 » » » 700кг/м3 2300-2700 » » » 600кг/м3 2700-3000 » » » 500кг/м3 и ниже г) плотность песчаного шламаиз грубомолотого песка должна быть не менее 1,6 кг/л. Плотность шлама песканормального помола (при вибрационном способе формования изделий) 1,68 кг/л;плотность шлама вторичных продуктов обогащения руд должна быть 1,75-1,8 кг/л. Таблица 1 2.4.Кислая зола-унос ТЭС с электрофильтров от сжигания углей должна иметьстекловидных и оплавленных частиц не менее 50 %; потери при прокаливании должныбыть не более 3 % для золы бурых углей и не более 5 % для золы каменных углей.Удельная поверхность зол бурого угля должна быть не менее 4000 см2/ги не более 5000 см2/г - длякаменноугольных. Зола должна выдерживать испытания на равномерность измененияобъема. 2.5.Карбонатные материалы следует применять с удельной поверхностью 2500-5000 см2/гв количестве 20-30 % массы цемента. 2.6.В качестве волокнистой добавки следует применять асбест 5-го и 6-го сортов,удовлетворяющий требованиям ГОСТ 12871-67*. 2.7.Вода должна удовлетворять требованиям ГОСТ 23732-79. 2.8.В качестве газообразователя должна применяться водная суспензия алюминиевойпудры. Водную суспензию следует изготавливать из алюминиевой пудры ПАП-1,отвечающей требованиям ГОСТ 5494-71, илипасты, приготовленной на основе пудры ПАП-1, в условиях, обеспечивающихвзрывобезопасность. 2.9.В качестве пенообразователя следует применять клееканифольный,смолосапониновый, ПО-6 и другие вещества, пена из которых удовлетворяеттребованиям п. 4.3 настоящей Инструкции. 2.10.Материалы для приготовления пенообразователей должны удовлетворять требованиям:клей костный - ГОСТ2067-71*, клей мездровый - ГОСТ 3252-75*, канифольсосновая - ГОСТ19113-73, натр едкий - ГОСТ 2263-71*. 2.11.Химические добавки и поверхностно-активные вещества (ПАВ), применяемые длярегулирования процесса структурообразования, нарастания пластической прочностии ускоренного твердения ячеистобетонной смеси, а также и для ее пластификации,должны удовлетворять требованиям: гипсдвуводный - ГОСТ4013-74, поташ - ГОСТ 4221-76, содакальцинированная - ГОСТ 5100-73*,триэтаноламин, тринатрийфосфат, жидкое стекло - ГОСТ 13078-67*,сульфанол, детергент советский марки ДС-РАС, контакт нефтяной черныйрафинированный марки КНЧР. Расход химических добавок вПАВ должен назначаться в зависимости от вида вяжущего и уточняться опытнымпутем. 2.12.Арматурная сталь для арматурных каркасов, сеток и закладных деталей должнаудовлетворять требованиям ГОСТ10922-75. 2.13.Выбор материалов для защиты арматуры от коррозии, защитно-отделочных слоев ипокрытий стеновых изделий и составных панелей, технология их изготовлениядолжно назначаться в соответствии с требованиями разделов 3 и 9,а также приложений 1и 3настоящей Инструкции. 3. ЗАЩИТА АРМАТУРЫ ОТ КОРРОЗИИ 3.1. Арматурныекаркасы и сетки в изделиях из ячеистого бетона необходимо защищатьантикоррозионными покрытиями. Поверхности каркасов и сеток перед нанесениемпокрытия должны быть сухими, без следов ржавчины и масла. 3.2.В качестве антикоррозионных покрытий следует применять холоднобитумную,цементно-полистирольную, горячую ингибированную сланцебитумную цементную илилатексно-минеральную мастики. Приготовление и нанесение мастик должныпроизводить в соответствии с прил.1. 3.3.Мастика, нанесенная на каркасы и сетки, должна быть высушена в естественныхусловиях или подогретым воздухом и должна выдерживать транспортировку и укладкув формы без поврежденной сплошности покрытия. 3.4.Антикоррозионные покрытия должны удовлетворять следующим требованиям: прочность на удар не менее10 кг/см2 по ГОСТ4765-73; эластичность не более 20 ммпо ГОСТ 10086-77; при косом срезе острым ножомвдоль поверхности арматуры не должно происходить отслоения покрытия запределами среза. 3.5.Если сплошность покрытия на каркасе нарушена, он должен подвергаться повторнойзащите. 3.6.Закладные детали в изделиях должны быть защищены металлизационными алюминиевымипокрытиями со специальной обработкой в соответствии с требованиями главы СНиП II-28-73«Защита строительных конструкций от коррозии» и с указаниями в рабочих чертежахна изделие. 4. ПОДБОР СОСТАВА ЯЧЕИСТОБЕТОННОЙ СМЕСИ 4.1.Подбор состава ячеистобетонной смеси должен производиться лабораторией предприятияпри изменении требований проектных характеристик бетона или исходного сырья итехнологии производства. Кроме того, в процессе работы предприятия лабораториядолжна производить корректировку состава смеси в связи с возможными колебаниямисвойств сырья. Таблица 2 - 4.6.Пористость Пг следуетрассчитывать по формуле (3) где gс - заданная объемная массаячеистого бетона в сухом состоянии, кг/м3; Кс - коэффициент увеличениямассы ячеистого бетона за счет связанной воды; W - удельныйобъем сухой смеси, л/кг; В/Т - водотвердое отношение. 4.7.Удельный объем сухой смеси следует определять на основании опытного замеса ирассчитывать по формуле (4) гае - фактическаяобъемная масса растворной смеси. 4.8.В качестве исходных значений при расчетах по формулам (2) и (3) принимают: Кс = 1,1; a = 0,85; К= 1390 л/кг при использовании алюминиевой пудры и К = 20 л/кг при использовании пены. 4.9.Расход материалов на замес определяют по формулам: (5) (6) (7) (8) (9) (10) (11) где Рсух -расход материалов на замес, кг; gс - объемная масса ячеистогобетона, высушенного до постоянного состояния, кг/м3; Кс - коэффициент увеличениямассы в результате твердения за счет связанной воды. Для предварительныхрасчетов принимают равным 1,1; V - заданный объемодновременно формуемых изделий, увеличенный с учетом образования «горбушки» на7-10 % для индивидуальных форм и 3-5 % для массивов, л; Рвяж -масса вяжущего, кг; Рц -масса цемента, кг; n -доля цемента в смешанном вяжущем; Ри - масса извести, содержащей100 % СаО, кг; Риф -масса извести с фактическим содержанием СаО, кг; Аф - фактическое содержаниеСаО в извести, %; Рв -масса воды, кг; Рк - масса кремнеземистогокомпонента, кг. 4.10.На основании соответствия результатов испытаний образцов из опытных замесовячеистобетонной смеси требуемым показателям по объемной массе и прочности присжатии ячеистого бетона следует назначать рабочий состав ячеистобетонной смеси. 4.11.После производственной проверки рабочего состава ячеистобетонной смеси должныбыть составлены таблицы расхода материалов на 1 м3 бетона и назамес, а также технологические карты производства изделий. 5. ПРИГОТОВЛЕНИЕ ЯЧЕИСТОБЕТОННОЙ СМЕСИ 5.1.Приготовление газобетонной смеси следует производить в гидродинамическомсмесителе или вибросмесителе СМС-40Б. 5.2.Последовательность загрузки материалов в гидродинамический смеситель длягазобетонной смеси должна быть следующей: песчаный шлам + вода + вяжущее +добавки или вода + сухой песок + вяжущее + добавки. После 2 мин перемешивания всмеситель подают заданное количество водной суспензии алюминиевой пудры, исмесь перемешивают еще 1-2 мин. 5.3.Последовательность загрузки материалов в вибросмеситель должна быть следующей:сначала загружают песчаным шлам и воду и перемешивают 30 с, затем добавляютвяжущее и водную суспензию алюминиевой пудры. Интенсивность виброперемешиваниядолжна быть 300 -1000 см2/с3. 5.4.Приготовление пенобетонной смеси следует производить в двухбарабаннойпенобетономешалке СМ-578. В одном барабане из водного раствора пенообразователяв течение 5 мин приготавливают пену, в другом в течение 5 мин раствор извяжущего, кремнеземистого компонента и воды. Пену выгружают в барабан сраствором, и смесь перемешивают не менее 2 мин. Пенобетонная смесь несколькихзамесов выгружается для усреднения в промежуточный бункер, затем в раздаточныйкюбель для заполнения форм. В промежуточном бункере пенобетонная смесь недолжна находиться более 20 мин. 5.5.Дозирование вяжущего и кремнеземистого компонента следует производить по массевесовыми дозаторами с точностью ±1 % для вяжущего и ±2 % для кремнеземистогокомпонента. 5.6.При добавлении в ячеистобетонную смесь асбеста (3-5 % массы сухих материалов)его необходимо предварительно распушить в смесителе. Смесители должныпромываться после каждой рабочей смены и при длительных перерывах в работе. 6. ФОРМОВАНИЕ ИЗДЕЛИЙ 6.1.Формование изделий следует производить в соответствии с технологической схемойпринятого способа производства. 6.2.Стальные формы для формования изделий или крупных массивов должны удовлетворятьтребованиям ГОСТ 13886-73* и других действующих стандартов на стальные формы.Поддон и бортоснастка должны быть тщательно очищены, смазаны и подогреты дотемпературы 40°С.При формовании изделий с применением отделочного материала, укладываемого надно формы, поддон не смазывается. 6.3.Для смазки форм следует применять материалы следующих составов: петролатумно-керосиноваясмесь: 1 часть петролатума и 2,5 части керосина; солидол (ГОСТ 4366-76) илиавтол в смеси с керосином в соотношении по массе 1:1; смесь кулисного и машинногомасел в соотношении по массе 1:3. Смазку следует наносить израсчета 150 г на 1 м2 смазываемой поверхности форм. 6.4.При установке в формы арматурные каркасы, сетки и закладные детали не должныиметь искривлений стержней и механических повреждений. Укрупнительную сборкукаркасов следует производить в специальных кондукторах. Закладные детали иарматурные каркасы должны быть закреплены в форме для предупреждения их сдвигаво время заливки ячеистобетонной смеси и ее вспучивания. Отклонение от проектногоположения размещения арматурного каркаса в форме не должно превышать допустимыхпределов, указанных в ГОСТе или рабочих чертежах на изделия. 6.5.Для обеспечения требуемой толщины защитного слоя бетона (не менее 25 мм)арматурные каркасы и сетки следует размещать на подкладках-фиксаторах. 6.6.Форму следует заполнять за один прием. Высоту заполнения формы газобетоннойсмесью h следует рассчитывать поформуле (12) где Kг - коэффициент, учитывающийвысоту «горбушки» после вспучивания; h0 - высота формы, см; gя - объемная массагазобетонной смеси, кг/л; gр - объемная масса растворнойсмеси, кг/л. При литьевом способеформования коэффициент Кг принимают равным 1,1 и1,05 при вибрационном и при литьевом способе формования массивов высотой 60 см. 6.7.При формовании изделий или массивов по литьевому способу необходимо соблюдатьследующие требования: а) при изготовлении изделийс отделочным слоем из поризованного раствора с добавкой ПО-6 и СНВ заливкагазобетонной смеси на этот слой должна производиться не ранее 30 мин и непозднее 1 ч после его укладки; при заливке непосредственно на ковры с керамическойили коврово-мозаичной стеклянной плиткой - не ранее 30 мин после окончанияфиксации ковров, в форме; б) формы с ячеистобетоннойсмесью после вспучивания следует выдерживать на постах заливки при температуре15-20°С до приобретения требуемойпластической прочности. Для ускорения достижения требуемой пластическойпрочности формы со смесью следует выдерживать 1,5-2 ч в термокамерах притемпературе 70-80°С.Контроль пластической прочности ячеистобетонной смеси осуществляют при помощипластомера (прил.2); в) образовавшуюся послевспучивания газобетонной смеси «горбушку» срезают или прикатывают. Срезка«горбушки» должна осуществляться механизированным способом при достиженииповерхностным слоем пластической прочности в 100-150 г/см2, прикатка«горбушки» - при пластической прочности поверхностного слоя 150-200 г/см2. 6.8.Формование газобетонных изделий вибрационным способом следует производить в соответствиис «Инструкцией по изготовлению изделий из ячеистого автоклавного бетона покомплексной вибрационной технологии». 6.9.Отходы ячеистого бетона-сырца, полученные в результате срезки «горбушки» иразрезки массива должны перемешиваться с водой в растворомешалке иперекачиваться в специальный шламбассейн для повторного использования. 6.10.Изделия из пенобетонной смеси, формуемые литьевым способом, следует передтепловлажностной обработкой выдерживать в помещении при температуре воздуха18-20°С не менее 8 ч. При этомповерхность изделий необходимо предохранять от интенсивного высыхания. 6.11.Подъем, транспортировку и укладку на вагонетки форм с отформованными изделияминеобходимо производить шарнирными траверсами, предотвращающими перекос форм.Применение гибких строп не допускается. Подъем массива ячеистогобетона-сырца следует производить захватами, обеспечивающими необходимые условияобжатия массивов ячеистого бетона-сырца в период извлечения его из форм иподачи на стол резательной машины. 6.12.При изготовлении изделий по резательной технологии необходимо учитыватьследующие требования: а) поверхности плоскостейдна формы и стола резательной машины не должны иметь перепады более чем на 1мм/м для мелкоштучных неармированных изделий и 0,4 мм/м для крупноразмерныхармированных изделий; б) подъем и опусканиемассива должны осуществляться плавно, без резких толчков и ударов; в) до снятияпредварительного обжатия массив ячеистого бетона-сырца должен равномерноприлегать к поверхности рабочего стола резательной машины, а масса захватадолжна передаваться на фиксирующее устройство; г) для предотвращениянеравномерного изменения пластической прочности ячеистобетонной смеси по всемуобъему массива, время выдержки с момента раскрытия бортов формы до его разрезкине должно превышать 10 мин. 6.13.Пластическая прочность ячеистобетонной смеси в массиве к началу разрезки должнабыть 300-350 г/см2. В случае подъема массива с бортами формыпластическая прочность измеряется в середине «горбушки». 6.14.До открытия бортов формы необходимо снять кондуктор, фиксирующий арматурныекаркасы. Величина предварительногообжатия в нижней плоскости массива (на уровне 1/3 еговысоты) должна быть 250-300 г/см2. 6.15.Для продольно-вертикальной и горизонтальной разрезки следует применятьустройства, оборудованные гладкими струнами диаметром 0,8-1,2 мм из пружиннойпроволоки класса I по ГОСТ9389-75. Скорость резания должнасоставлять 5-7 м/мин. Если режущие струны совершают колебательные движения иотсутствуют упоры в зоне выхода струн из массива, скорость резания должна бытьне более 0,15 м/мин. 6.16.При поперечной разрезке должны применяться резательные устройства сколебательными движениями струн. При разрезке «снизу вверх» следует применятьгладкие струны диаметром 0,8-1 мм. При разрезке «сверху вниз» следует применятьструны диаметром до 1,2 мм со спиральной навивкой из струны диаметром 0,3-0,5мм. Поперечную разрезку «снизу вверх» осуществляют перед продольно-вертикальнойи горизонтальной разрезкой. 6.17.При горизонтальной разрезке массива ячеистого бетона-сырца больше чем на трех уровнях режущие струны следуетустанавливать на расстоянии не менее 400 мм друг от друга. Количество струн,устанавливаемых одна под другой, должно быть таким, чтобы местное опусканиепакета разрезанных изделий в одной вертикальной плоскости не превышало 2-3 мм. Одновременно спродольно-вертикальной и горизонтальной разрезкой следует производитькалибровку боковых поверхностей, вырезку пазов и снятие фасок. «Горбушку» следует удалятьодновременно с продольной и горизонтальной разрезкой массива ячеистогобетона-сырца. 7. ТЕПЛОВЛАЖНОСТНАЯ ОБРАБОТКА РАСПАЛУБКАИЗДЕЛИЙ 7.1.Для твердения отформованных изделий следует применять автоклавную обработку,пропаривание или электропрогрев. Пропаривание и электропрогрев следуетприменять только для изделий, изготовленных на основе цемента или доменныхшлаков. Допускается двухстадийная тепловлажностная обработка изделий - сначалапропаривание, а затем автоклавная обработка. 7.2.В начальный период запаривания из автоклава следует удалить воздух продувкойпаром. Повышение температуры в автоклаве до 100-105°С должно производитьсяравномерно в течение 0,7-1,5 ч. Время продувки автоклава можно увеличить додостижения в центре изделия температуры 70°С и более. Пар в автоклав следуетподавать через детурбуляционное устройство. 7.3.Режимы автоклавной обработки представлены в табл. 5; они могут быть уточнены в заводских условиях сучетом специфических свойств применяемых материалов. Допускается применениеавтоклавной обработки при пониженном давлении пара при условии полученияячеистого бетона с физико-техническими свойствами, отвечающими требованиям действующих ГОСТ на изделия, атакже, если это экономически оправдано для производства. Не допускаются спадыдавления в период подъема, выдержки. Колебания давления в автоклаве не должныпревышать 0,2 ат. Процесс управления режимом автоклавной обработки должен бытьавтоматизирован. 7.4.Величина минимально допустимого остаточного давления в автоклаве (максимальногонаружного избыточного давления) должна быть указана в паспорте автоклава или вразрешении завода-изготовителя на его эксплуатацию в условиях разряжения. Таблица5 Примечание. В графе 8 над чертой дана продолжительностьавтоклавной обработки при начальной температуре более 70°Св центре изделия к моменту выдержки; под чертой - продолжительность автоклавнойобработки при начальной температуре менее 70°С. 7.5.При кассетном способе производства газобетонных изделий перед автоклавнойобработкой следует проводить пропаривание изделий в кассетах в течение 7 ч дляприобретения газобетоном прочности при сжатии не менее 5 кгс/см2.Пар в кассету следует подавать через 2 ч после вспучивания газобетона. Прииспользовании многоместных кассет пропаривание следует вести по режиму 2+2+3 ч,а при двухместных - по режиму 2+4+1 ч (подъем температуры в бетоне до 95-100°С + прогрев с подачей пара +охлаждение при закрытых бортах). Распалубку изделий и переносих на автоклавные вагонетки следует производить сразу после окончанияпропаривания. 7.6.При пропаривании в индивидуальных формах изделий из ячеистого бетона,изготовленного с применением портландцемента, температура выдержки впропарочных камерах должна составлять 85±5°С, а со шлакопортландцементом 90±5°С. Режимы пропаривания изделийприведены в табл. 6. Таблица 6 Наружные слои и покрытия стеновых изделий и составных панелей Внутренние слои и покрытия стеновых изделий и составных панелей для помещений подверженных действию атмосферной влаги (надцокольные) в помещениях с сухим и нормальным влажностным режимом с влажным режимом с сухим и нормальным влажностным режимом В процессе формования в горизонтальных формах Раствор - 1800 кг/м3; Rсж - 120-150 кгс/см2; толщиной 25-30 мм Коврово-мозаичная стеклянная и керамическая плитки на виброгазобетоне или промежуточном слое из поризованного раствора Каменные дробленые материалы на ячеистом бетоне или промежуточном слое из поризованного раствора. Поризованный раствор (цветной, серый, рельефный) g = 1200-1400 кг/м3, Rсж - 100 кгс/см2 толщиной 20-25 мм. Рельефная поверхность ячеистого бетона с последующим нанесением покрытий Уплотнение „горбушки" с нанесением лакокрасочных материалов (5-7 слоев) Поризованный раствор толщиной 50-70 мм с последующих нанесением лакокрасочных материалов (2-3 слоя) Уплотнение «горбушки» После распалубки стеновых изделий и составных панелей Пропитка кремний-органической жидкостью 136-41 с последующей покраской Водоэмульсионные краски - Э-КЧ-112, Э-ВА-17, ПВАЦ; ЦПХВ. Краски ВН-30ДТС полимерцецентные. Декоративные присыпки по клею на основе эмульсии МБМ-5с и латекса СКС-65ГП (декор, КДОСИ, АЦС); по клею на основе дисперсии ПВА (Э-ВА.5189, ПВАЦ) и ее модификации (ПВАГ, ПВАМ, ПМС) Эмали КО-174, наполненные тальком. Цементные краски. Декоративный раствор (тонкослойная штукатурка). Гидрофобизация кремнийорганиче-ской жидкостью 136-41. Керамическая плитка, приклеенная полимерным клеем Эмали ХП-799. Краски МС-226. Краски ПВАЦ с повышенным содержанием полимеров. Перхлорвиниловые эмали ХС, лак ХС-76, эмаль ХС-710. Краски СПП, ПФ-115. Пропитка раствором битума и керосина Краски: силикатные, Э-КЧ-26, Э-ВА-17, Э-ВА-27, цементные (без стеарата кальция), обои 9.5.Коврово-мозаичную стеклянную плитку размером 22´22 мм (ГОСТ17057-80) со швом между плитками 5,5 мм, керамическую плитку (глазурованнуюи неглазурованную) размером 48´48 мм (ГОСТ 17657-72 и 13996-77)со швом не менее 7 и плитку типа «брекчия» следует укладывать на дно формы споследующей заливкой ее виброгазобетонной смесью или укладкой промежуточногослоя из поризованного раствора (при литьевом способе формования).Предварительно на дно формы следует укладывать крафт-бумагу (ГОСТ 8273-75). Ковры набумаге закрепляют клеем из галерты. Указанная ширина швов между плитками должнабыть сохранена и в период стыковки ковров в форме. При отделке торца изделийковер наклеивают на борт формы с одновременным перегибом и приклеиванием нижнейего части ко дну формы, а верхней - к горизонтальной плоскости борта. Приформовании стеновых изделий с отделкой по вибрационному способу время вибрациине должно превышать 5 мин. 9.6.Окончательную обработку наружной поверхности стеновых изделий (удалениемасляных пятен, бумаги, клея, песка, неприставших каменных материалов, вскрытиецементной пленки) производят после их распалубки. Для получения гладкойповерхности следует применять фрезеровальные машины, мозаично-шлифовальныеС-475 и С-420. Очистку бумаги, клея, песка и частиц каменных материаловпроизводят механическими щетками. 9.7. Отделку наружныхповерхностей стеновых изделий после распалубки и составных панелей следуетпроизводить готовыми водоэмульсионными стиролбутадиеновыми красками Э-КЧ-112 иполивинилацетатнымн Э-ВА-17 (ГОСТ20833-75), цементно-перхлорвиниловыми (ЦПХВ), органосиликатными ВН-30,эмалями на основе хлорсульфированного полиэтилена ХП-799 и кремнийорганическимиКО-174, а также приготавливаемыми на предприятии ячеистого бетона (согласно прил.3) поливинилацетатными красками различной модификации ПВАЦ, ПВАГ, ПМС,ПВАМ, цементными с добавкой дисперсии ПВА 50 %-ной (ГОСТ18992-73*) и декоративными присыпками (крошка стекла, мрамора, гранита идр.) фракцией 1,2-1,6; 1,7-2 мм по клею на основе дисперсии ПВА-Э-ВА-5189 иПВАЦ, на основе акриловой эмульсии МБМ-5с и синтетического латекса СКС-65 ГП (ГОСТ10564-75) - КДОСИ, Декор, АЦС. Кроме того, отделку производят декоративнымраствором толщиной 3 мм. Отделка должна производитьсяв помещениях с температурой воздуха не ниже +8°С. 9.8.Поверхность стеновых изделий, подлежащая отделке после распалубки, должнаотвечать требованиям ГОСТ11118-73. Влажность ячеистого бетона в поверхностном слое до 5 мм принанесении красок на органических растворителях должна быть не более 8 %.Влажность бетона при отделке водоэмульсионными красками и составами не ограничивается. 9.9. Поверхность изделий исоставных панелей, полученную после резки массива ячеистого бетона струной и неподвергающуюся дополнительной механической обработке до нанесениязащитно-отделочного покрытая, следует огрунтовать лаком ХВ-784 (ГОСТ7313-75*) или АК-113. 9.10. Систему наружныхзащитно-отделочных покрытий с гладкой и шероховатой фактурой следует назначатьпо табл. 10. 9.11.Систему наружных защитно-отделочных покрытий с декоративной присыпкой следуетназначать по табл. 11. 9.12.Состав водоэмульсионных грунтовок, шпаклевок, клея, закрепляющего илиотделочного слоев следует приготовлять в смесителях СБ-43, С-716, С-365, СО-11,С-411А, акустической быстроходной мешалке (АУРК). Составы на растворителяхследует приготовлять или разводить в герметически закрытых смесителях иликрасконагнетательных бачках С-383, С-764. Готовые составы должны бытьоднородны, не иметь сгустков, комков, загрязнений. 9.13.Грунтовочные и отделочные составы следует наносить при давлении 2-3 ат спомощью пистолетов-распылителей КРВ-2, О-45, С-592, соединенных скрасконагнетательным бачком С-411, или пистолета ГСХ (Р-68), установки С-562. Шпаклевочные составы сцементом, молотым песком или крупным наполнителем следует наносить из пистолетаГСХ (Р-68), при давлении 3-4,5 ат, установки С-562 и другими устройствами. Декоративные присыпкиследует наносить пневматическим распылителем типа «крошкомет» при давлении 1-2ат или электростатическим лотковым распылителем типа «Декостат» при напряжении80-110 кВт. 9.14. Гидрофобизацию поверхностиследует производить в один слой в окрасочных камерах при температуре воздуха нениже +5°Сраствором 10 %-ной водной эмульсии кремнийорганической жидкости 136-41 (ГОСТ10834-76) или 10 %-ным раствором жидкости 136-41, приготовленным путемрастворения ее в уайт-спирите (ГОСТ 3134-78) или керосине (ГОСТ4753-68*) в соотношении 1:9 (по массе), а также кремнийорганическими жидкостямиГКЖ-10 (ГОСТ 13032-77)или 5 %-ным раствором ГКЖ-11 (ГОСТ 13004-77).Сушку гидрофобизированной поверхности производят в течение 48 ч при температурене ниже +10°С,при более высокой температуре продолжительность сушки сокращается. Таблица10 - - - 9.15.Декоративный раствор вязкостью 14-18 см (по Суттарду) следует наносить в дваслоя на поверхность, огрунтованную эмульсией МБМ-5с, дисперсией ПВА 50 %-нойили латексом СКС-65ГП вязкостью 15-20 с по ВЗ-4 (марка грунтовки должнасоответствовать полимерной основе декоративного раствора). Состав и способприготовления даны в прил. 3. 9.16.Ковровую керамическую плитку (глазурованную и неглазурованную) после распалубкипанелей следует приклеиватьполимерцементным клеем состава, приведенного в прил. 3. 9.17.Отделку внутренних поверхностей при формовании стеновых изделий «лицом вверх»следует производить поризованным раствором согласно п. 9.2 настоящей Инструкции. Раствор следует укладывать надно формы слоем толщиной 50-70 мм. Заливку ячеистой смеси следует производитьне позднее 1 ч после укладки раствора. При формовании стеновыхизделий «лицом вниз» верхний слой свежеотформованного бетона необходимоуплотнить и после распалубки изделий нанести лакокрасочный материал илипропитать поверхность ячеистого бетона битумными составами. 9.18.Выбор системы защитных лакокрасочных покрытий для внутренних поверхностейизделий следует производить в соответствии с проектом и по табл. 7 настоящей Инструкции. 9.19.При нанесении защитных лакокрасочных покрытий необходимо пользоваться основнымиправилами производства и приемки работ, изложенными в главе СНиП II-28-73. 10. КОНТРОЛЬ КАЧЕСТВА ИЗДЕЛИЙ И ПРАВИЛА ИХПРИЕМКИ 10.1.Лаборатория предприятия обязана производить контроль и анализ качествапоступающих на предприятие материалов и полуфабрикатов. Отдел технического контроляпредприятия должен производить приемку готовых изделий, а также анализ причинбрака. 10.2.Поступающие на предприятие материалы и полуфабрикаты принимают партиями, приэтом в каждой партии проверяют по методикам, указанным в соответствующихГОСТах, технических условиях и настоящей Инструкции, следующие свойства: а) минералогический составцемента, вид гидравлической добавки и марку - по паспорту, тонкость помола,активность и сроки схватывания - по ГОСТ 310.1-76 - ГОСТ310.4-76; б) содержание С2О+ MgO в извести, содержание «пережога» - по прил. 4; срокигашения, тонкость помола - по ГОСТ 22688-77; в) тонкость помолаизвестково-песчаной смеси следует проверять в соответствии с прил.5; г) содержание ввысокоосновной золе СаО, SiO2, SO3 и суммарное количество (К2О+ Na2О) определяют химическим анализом; удельная поверхность - поПСХ; д) модули активности иосновности доменного гранулированного шлака - по паспорту; е) содержание в кварцевомпеске кварца, слюды, илистых и глинистых примесей - по ГОСТ 8735-75, ГОСТ5382-73; ж) дисперсность золы, потерипри прокаливании, набухание, содержание стекловидной фазы; и) фракционный составдекоративной присыпки - соответствие требованиям п.9.7 настоящей Инструкции; к) вязкость грунтовочных,шпаклевочных и закрепляющих составов,клеев и лакокрасочных материалов - соответствие требованиям пп. 9.9 и 9.10; л) марку и содержаниеактивного алюминия в алюминиевой пудре - по прил. 6; м) качество пенообразователя- по паспорту. 10.3. При контролепроизводственных процессов лаборатория проверяет: а) дисперсность песка, золы,гипса и других материалов в порядке, предусмотренном технологической картой, ноне реже одного раза в смену; б) плотность и температурушлама согласно прил. 7; в) текучесть поризованногоотделочного раствора и вязкость раствора, а также температуру, смеси в моментразлива ее в формы и после вспучивания (из каждого третьего замеса); г) объемную массуячеистобетонной смеси (в каждой третьей форме); е) высоту вспучивания смеси(в каждой третьей форме); ж) пластическую прочностьячеистого бетона-сырца перед прикаткой «горбушки» и резкой массива согласно прил.2; з) режим тепловлажностнойобработки изделий (для каждой запарки, пропарки); и) тщательность очистки исмазки форм и плотность закрытия бортов (в каждой форме); к) правильность нанесения надно формы подстилающего слоя песка, равномерность уложенных каменных,керамических материалов и коврово-мозаичных стеклянных плиток (один раз всмену); л) правильность технологииприготовления состава красок и клеящей основы (один раз в смену); м) свойствазащитно-отделочных покрытий 1 раз в квартал или при изменении материалов. 10.4.Для оценки стабильности технологических процессов на предприятии необходиморезультаты контроля качества материалов и производственных процессов ежемесячноподвергать статистической обработке, согласно прил.8 и сопоставлять их соответствие с нормируемыми показателями табл. 12. При изменении сырья ипараметров производства лаборатория обязана вносить необходимые коррективы втехнологию изготовления изделий. 10.5.При приемке готовых изделий проверке ОТК подлежат: а) объемная масса, прочностьпри сжатии ячеистого бетона, поризованного раствора в изделиях (в каждойпартии); б) влажность изделий (вкаждой партии); в) морозостойкость ячеистогобетона и поризованного раствора (при изменении состава бетона, раствора); г) размеры изделий, толщиназащитного слоя арматуры, наличие, выколов, трещин и других видимых дефектов (вкаждой партии); Таблица12 11. ХРАНЕНИЕ И ТРАНСПОРТИРОВАНИЕ ИЗДЕЛИЙ 11.1.Готовые изделия из ячеистого бетона должны быть защищены от увлажнения ихраниться на крытом складе или под навесом в соответствии с требованиями ГОСТ11118-73, ГОСТ19570-74, ГОСТ 5742-76. 11.2.Стеновые изделия и составные панели должны храниться в кассетах в вертикальномположении. Стойки кассет следует размещать от торца панели на расстояние неменее 0,2 м. При транспортированиистеновые панели из ячеистого бетона объемной массы 600 кг/м3 именее, а также все панели с отделочным слоем следует устанавливать ввертикальном положении в специальные контейнеры. Зазор между изделиями ипанелями должен быть 30-50 мм. 11.3.Панели перекрытий должны храниться на деревянных прокладках в штабелях, имеющихне более шести рядов по высоте. Зазор между панелями должен быть не менее 30мм. 11.4.Теплоизоляционные изделия, рассортированные по маркам, следует хранить вконтейнерах. При отсутствии контейнеров в штабелях не более шести рядов повысоте с деревянными прокладками толщиной не менее 25 мм и шириной 70 мм. 11.5.Погрузку и выгрузку изделий следует производить специальными подъемнымимеханизмами. Пластическую прочностьгазобетонного сырца следует определять с помощью переносного коническогопластометра пружинного типа. Перед определениемнеобходимо проверять плавность перемещения конуса и нулевое положение стрелкииндикатора. Не допускается к применению индикатор с отклонением стрелки отнулевого показания более ±0,05мм или индикаторы со свободно перемещающимся стержнем. Пластическая прочностьгазобетона-сырца должна определяться на верхней грани изделия на расстоянии неменее 20 см от борта формы. Поверхность бетона в месте испытания должна бытьровной без каверн и включений твердых частиц. Место и время определения пластическойпрочности должны быть указаны в технологической карте. При замере конусустанавливают перпендикулярно поверхности бетона и медленно вдавливают рукой всырец до полного погружения, при этом следует брать показания с точностью до0,1 мм. Пластическую прочность сырцаRпл, кгс/см2, вычисляют по формуле (13) где Р - жесткостьпружины, кгс/см; п - показание индикатора, см. Величину пластическойпрочности следует определять как среднее арифметическое из трех испытаний.Описание пластометра непружинного типа и правила пользования приведены в«Инструкции по изготовлению изделий из ячеистого автоклавного бетона покомплексной вибрационной технологии».
Рабочий проходит инструктажи по охране труда. Контейнеры для кирпича, бетонные блоки и другие материалы и изделия должны.
Фундаментные блоки (ФБС) Инструкция по охране труда при работах с бетоном : Явления вибрационной болезни, вызванные воздействием общей и местной вибрации при изготовлении железобетонных изделий, носят.
Охрана окружающей среды 30 6. Требования безопасности труда и производственная санитария 32 6.1. предназначенный для изготовления блоков стеновых мелких и изделий теплоизоляционных, 08.06.2007 СН 277-80 ИНСТРУКЦИЯ ПО ИЗГОТОВЛЕНИЮ ИЗДЕЛИЙ ИЗ ЯЧЕИСТОГО БЕТОНА.
Новости охраны труда |; Статистика ОТ СН 277-80 « Инструкция по изготовлению изделий из ячеистого бетона » В качестве вяжущих для приготовления ячеистого бетона следует применять. После отделки поверхности изделий,установки оконных блоков, подоконников и т.п. производят повторное.

ОХРАНА ТРУДА, ТЕХНИКА БЕЗОПАСНОСТИ И ПРОТИВОПОЖАРНЫЕ. Для изготовления конструкций из ячеистого силикатного бетона. СН 529- 80 Инструкция по технологии изготовления конструкций и изделий из плотного.


ВСН 02-74 - Инструкция по определению прочности бетонных сооружений СССР - Инструкция по изготовлению двухслойных стеновых панелей и блоков из ВСН 203-84 - Правила по технике безопасности при возведении.
государственный комитет украинской сср по делам строительства научно-исследовательский институт строительных конструкций госстроя ссср ТЕХНОЛОГИЯ ИЗГОТОВЛЕНИЯ БЛОКОВ ИЗ КОНСТРУКТИВНОГО ЯЧЕИСТОГО СИЛИКАТНОГО БЕТОНА АВТОКЛАВНОГО ТВЕРДЕНИЯ ДЛЯ СТЕН ЖИЛЫХ И ГРАЖДАНСКИХ ЗДАНИЙ КИЕВ 1986 Настоящие республиканские строительные нормы содержат требования к исходным материалам, их подготовке и переработке, составу бетонной смеси и методам его подбора, приготовлению смеси и формованию изделий, защите арматуры от коррозии, тепловлажностной обработке. Приведены правила контроля производства, качества изделий и их приемки. Рассчитаны на инженерно-технических работников заводов по производству крупноразмерных изделий и конструкций из ячеистых бетонов автоклавного твердения. Разработаны НИИСК Госстроя СССР (кандидаты техн. наук В.А. Критов, В.И. Скатынский. Е.И. Чикота, инженеры С.М. Финкельштейн, В.А. Кабанов, В.Н. Макарук, В.Е. Петренко) и комбинатом "Ворошиловградхимстрой" Минтяжстроя УССР (инженеры В.Ф. Волошин, Ф.К. Ситенко, Б.А. Ярыш). 1. ОБЩИЕ ПОЛОЖЕНИЯ 1.1. Настоящие республиканские строительные нормы распространяются на технологию производства крупноразмерных стеновых блоков из конструктивного ячеистого силикатного бетона для жилых и гражданских зданий. Примечание . Конструктивный ячеистый бетон - искусственный каменный материал мелкопористой структуры, получаемый в результате твердения затворенной водой и перемешанной до однородного состояния смеси, состоящей из тонкомолотой извести, молотого и немолотого песка, порообразователя и регулятора гидратации извести. Для повышения некоторых физико-механических характеристик бетона взамен части извести в смесь вводят соответствующее количество клинкерного цемента. Плотность такого бетона в высушенном состоянии 1200 кг/м3. 1.2. Для бетонных и железобетонных конструкций, на изготовление которых распространяются требования настоящих РСН, должны предусматриваться следующие классы (марки) бетона: По прочности на сжатие ……………………………………В7,5 (М100), B10 (M150) По морозостойкости ………………………………………...Не ниже марки F35 Примечание. За класс (марку) бетона по прочности на сжатие принимается сопротивление осевому сжатию Р, кгс/см2, эталонного образца-куба с ребром 15 см, изготовленного из той же смеси, что и изделия, прошедшие автоклавную обработку одновременно с формуемыми изделиями и испытанные по ГОСТ 10180-78* при температуре 20 ± 2°С. Прочность бетона может определяться и на образцах-кубах с ребром 10 и 7,07 см, а также на цилиндрах диаметром и высотой соответственно 14; 10 и 7 см. Проектная марка бетона по морозостойкости означает число выдерживаемых циклов замораживания и оттаивания образцов, изготовленных согласно ГОСТ 10060 -76 и испытанных по ГОСТ 12852.4-77. 1.3. Механические и физические характеристики конструктивного ячеистого бетона определяются по результатам испытания не менее трех одинаковых по размеру контрольных образцов. Предел прочности бетона на сжатие вычисляется для каждого образца с точностью до 0,1 кгс/см2: , где Р - разрушающая нагрузка, кгс; F - средняя рабочая площадь образца, см2; α - переводной коэффициент к прочности эталонного образца размерами 15 ×15 ×15 см; K w - переводной коэффициент к прочности эталонного образца с влажностью по массе 10 ±2 %. 1.4. Значения переводного коэффициента α принимаются в зависимости от номинальных размеров образцов, см: 1.5. Конструкции и изделия рассчитывают по СНиП 2.03.01-84. 1.6. Толщины наружных стен жилых и общественных зданий из конструктивного ячеистого силикатного бетона принимаются в соответствии с требованиями СНиП II-3-79. При расчете толщины наружных стен используются величины, определенные по ГОСТ 7076-78. 2. МАТЕРИАЛЫ И ТРЕБОВАНИЯ К НИМ 2.1. Для изготовления конструкций из ячеистого силикатного бетона используются комовая известь, портландцемент, кварцевый песок, газообразователь, добавки для регулирования сроков схватывания и твердения ячеистобетонной смеси, вода, арматурная сталь, материалы для защиты арматуры от коррозии. 2.2. Комовая известь по п. 2.1 должна удовлетворять требованиям ГОСТ 9179-77. Содержание активных СаО+ М gО в извести - не менее 60 %, количество "пережога" - не более 2 %, скорость гашения 8...25 мин. До начала приготовления бетонной смеси известь должна содержать не более 20 % гидратированных частиц. 2.3. Портландцемент должен отвечать ГОСТ 10178-76*. В производстве необходимо использовать средне- и низкоалюминатные цементы (содержание трехкальциевого алюмината в клинкере не более 6 %) с началом схватывания не позднее 2 и концом 6 ч. 2.4. В качестве заполнителя применяется кварцевый песок по ГОСТ 8736-77*, содержащий не более 5 % глинистых и илистых примесей, слюды до 0,5 %. Модуль крупности песка не более 1,5. По содержанию органических примесей (колориметрическая проба) - не темнее цвета эталона. 2.5. Порообразователь (алюминиевая пудра ПАП-1 в соответствии с ГОСТ 5494-71*E) рекомендуется применять в виде гидрофильной пасты, поставляемой заводом-изготовителем. При отсутствии централизованной поставки допускается приготовление ее на заводе-потребителе при условии смешивания алюминиевой пудры с водным раствором сульфанола в соотношении по массе 1:1 (в 1л раствора - 25 г сульфанола) в металлической емкости, в которой поставляется алюминиевая пудра, или в специальной смесительной установке ЭКБ ЦНИИСК им. Кучеренко*. Пересыпание пудры в другую емкость не допускается. ___________ *См. "Руководство по изготовлению и применению алюминиевой пасты в качестве газообразователя для ячеистых бетонов" (М.: НИИЖБ, 1977). 2.6. Для регулирования процессов схватывания и твердения в ячеистобетонную смесь следует вводить в качестве добавки полуводный гипс ( ГОСТ 125-79). 2.7. Вода должна удовлетворять ГОСТ 23732-79. 2.8. Арматурная сталь для армированных изделий из конструктивного ячеистого силикатного бетона принимается согласно ГОСТ 10922-75, дополнительным указаниям рабочих чертежей на изделия при наличии заводского сертификата с указанием ее марки. Контрольные испытания производятся по ГОСТ 12004-81. Применение арматурной стали со следами ржавчины, грязи и масла не допускается. 2.9. Арматуру в изделиях из ячеистого бетона необходимо защищать антикоррозионными покрытиями независимо от вида применяемого вяжущего, плотности бетона и условий эксплуатации изделий и конструкций. 2.10. В качестве защитного покрытия арматуры ( приложение 2) рекомендуется использовать цементно-полистирольную мастику, для приготовления которой применяются: портландцемент ( ГОСТ 10178-76*); полистирол общего назначения ( ГОСТ 20282-74*); молотый песок с удельной поверхностью 2500...3000 см2/г (по ПСХ-2); скипидар ( ГОСТ 1571-82) или ксилол ( ГОСТ 9949-76*). 2.11. Для смазки форм используются отработанные машинные масла (нигрол, солидол, автол и др.). 2.12. Завод-изготовитель обязан производить проверку соответствия качества поступающих материалов требованиям государственных стандартов. 2.13. Материалы, поступающие на завод, должны храниться в условиях, исключающих их порчу. 3. ПОДГОТОВКА МАТЕРИАЛОВ 3.1. Подготовку материалов необходимо вести в соответствии с требованиями настоящего раздела. 3.2. Транспортировку и хранение извести на заводе-потребителе следует осуществлять в условиях, исключающих ее гидратацию в пушонку от действия ливневых и грунтовых вод. Сроки ее хранения на заводских складах устанавливаются опытным путем. 3.3. Перед помолом известь дробится на куски размером не более 25 мм. Помол производится с добавкой кремнеземистого компонента (3...5 % от массы извести). Удельная поверхность молотой извести должна быть не ниже 4500 см2/г (по ПСХ-2). 3.4. Кремнеземистый компонент (кварцевый песок) подготавливается следующим образом: часть его, вводимая в бетонную смесь без предварительного измельчения, просеивается перед подачей в расходные бункеры газобетономешалки через сито с отверстиями диаметром 10...15 мм; тонкодисперсный кремнеземистый компонент размалывается по мокрому способу до удельной поверхности 2200...2400 см2/г. Плотность песчаного шлама - в пределах 1,65...1,7 кг/л. Для повышения устойчивости шлама от расфракционирования целесообразно при помоле песка вводить в мельницу известь в количестве 2...3 % от массы песка ( приложение 1). 3.5. Суспензию алюминиевой пудры приготовляют перемешиванием в мешалке пасты с водой в соотношении 1:30 по массе в течение 2...3 мин до получения однородной смеси. Допускаются изготовление алюминиевой суспензии иных составов и применение других смесительных установок при условии обеспечения безопасности ведения работ и выполнения требований, предъявляемых к качеству ячеистого бетона. 3.6. Введение в бетонную смесь регуляторов гидратации перед подачей вяжущих значительно повышает их эффективность, дает возможность управлять процессами вспучивания и "созревания" бетона независимо от свойств используемого вяжущего и др. Поэтому твердые регуляторы гидратации (полуводный гипс) следует при необходимости домалывать в отдельной шаровой мельнице небольших размеров до тонкости помола не более 5 % остатка на сите № 02. 3.7. Арматурные сетки и каркасы изготовляются в соответствии с рабочими чертежами. Стержни арматуры, используемые для этого, при необходимости очищаются от загрязнения, ржавчины, масел. 3.8. Поверхность арматуры (сетки, каркасы и отдельные стержни) покрываются защитными антикоррозионными обмазками ( приложение 2). 3.9. Сетки и каркасы, защищенные антикоррозионными покрытиями, выдерживают до укладки в формы на специальных стеллажах. Транспортировку, укладку сеток и каркасов производят в условиях, исключающих повреждение защитного слоя. Сроки хранения арматуры с защитными покрытиями устанавливаются опытным путем. 4. ПОДБОР СОСТАВА БЕТОНА 4.1. Состав смеси для изготовления изделий из конструктивного ячеистого силикатного бетона назначают в зависимости от проектной марки бетона по прочности на сжатие и других физико-механических свойств с учетом качества сырья, условий производства и температурно-влажностного состояния окружающей среды. Рабочий состав бетона уточняется до начала массового изготовления изделий по экспериментально-расчетным данным. 4.2. Смесь, принимаемая в производство, должна обладать: текучестью, обеспечивающей вытекание смеси из резервуара газобетономешалки и равномерное распределение ее в форме; вспучиванием без расфракционирования смеси (при этом приростом объема за счет вспучивания должно обеспечиваться получение бетона проектной плотности); схватыванием за приемлемый промежуток времени; пластическая прочность схватившейся бетонной смеси - не ниже 0,5 кгс/см2; способностью приобретать в процессе запаривания проектную прочность на сжатие и пр. 4.3. Текучесть смеси и кинетика ее изменения во времени зависят от величины В/Т, содержания и вида вяжущего, а также регулятора гидратации (табл. 1). Таблица 1 На кинетику изменения текучести смеси во времени существенное влияние оказывают также начальная температура воды и других составляющих бетонной смеси и температурные условия в помещении, где формуются и "созревают" изделия. 4.4. Смесь ячеистого бетона, содержащая часть немолотого кварцевого заполнителя, приготовляется при В/Т = 0,25...0,34. 4.5. В оптимальных условиях смесь для формования изделий из ячеистого конструктивного силикатного бетона должна иметь достаточную текучесть в течение 10...15 мин с момента выхода из газобетономешалки. Текучесть регулируют введением в смесь регулятора гидратации - полуводного гипса (табл. 2). Таблица 2 4.6. Для бетонов классов от В7,5 до B10 (M100...M150) применяются смеси, содержащие 12...14 % активной СаО от массы сухих. При использовании смешанного (известково-цементного) вяжущего вместо соответствующего количества валовой извести в бетонную смесь вводится цемент. 4.7. Состав бетонной смеси и затраты материалов на 1 м3 бетона (в сухом состоянии) определяют экспериментально-расчетным путем, задаваясь плотностью бетона, соотношением молотого и немолотого заполнителя, активностью бетонной смеси по содержанию СаО + М gО, а также расходом газообразователя (г/кг сухих составляющих бетонной смеси). 4.8. Величину В/Т и расход регулятора гидратации принимают ориентировочно (см. табл. 1 и 2). 4.9. Для расчета устанавливают процентное содержание свободных СаО + М gО в извести, температуру и скорость гашения извести согласно ГОСТ 22688-77. 4.10. Потребность в материалах, кг. затрачиваемых на 1 м3 сухого бетона ( приложение 4), определяют по следующим формулам: где Иа- количество активной CaO; Ив - то же, валовой извести; Вх - потребность в химически связанной воде в бетоне: Г - количество регулятора гидратации; Пм, Пкар, потребность в кварцевом заполнителе, молотом заполнителе, сухом немолотом, немолотом в естественно-влажном состоянии соответственно; Q - сухие составляющие бетонной смеси; Р - масса 1 м3 бетона в высушенном состоянии, кг; Ам - активность смеси по СаО, % ; Ап - содержание активных СаО+М gО в извести, %; а - содержание регуляторов гидратации в смеси, % от массы СаО (см. табл. 2); у - долевое содержание молотого заполнителя. %; 0,15 - коэффициент, характеризующий содержание воды, %, в соединениях типа СаО·SiО2·nН2O и CaO H2O в сухом бетоне. Потребность в газообразователе на 1 м3 бетона определяют но формуле A l -n = δQ, г, где δ - затраты газообразователя на 1 кг сухих составляющих бетонной смеси. Суммарный расход воды на 1 м3 бетона, л: Вобщ = QB/T. Количество воды, кг, вводимой в бетонную смесь с немолотым заполнителем, Взап = Пкар- Дополнительная потребность, кг, в воде Вдоп = Вобщ - Взап 4.11. Состав бетонной смеси назначается в соответствия с требованиями, предъявляемыми к изделиям по несущей способности, долговечности и другим физико-механическим характеристикам в такой последовательности: по проекту принимают плотность и класс (марку) бетона; вычисляют затраты материалов на 1 м3 бетона; содержание активных СаО + М g О - в пределах 12...14 % от массы сухих; смесь для бетона класса В7,5 (M100) должна содержать 12...13 % активной CaO, B10 (M150) - соответственно 13...14 %; по табл. 1 принимают ориентировочно соотношение долей немолотого и молотого кварцевого заполнителя и величину В/Т; содержание регулятора гидратации - по табл. 2; затраты алюминиевой пудры - в пределах от 0,1 до 0,15 г/кг сухих; устанавливают текучесть бетонной смеси и кинетику ее изменения во времени; определяют плотность и свободную воду бетона на трех кубах, отформованных из смеси оптимального состава; ожидаемую плотность сухого бетона рассчитывают по формуле: ρбет = Робр (100- W б) /100 Vобр, где Робр - масса сырого образца, кг; Wб - влагосодержание сырого бетона, %; Voбp - объем образца, м3; изменением содержания газообразователя, регуляторов гидратации и варьированием величины В/Т корректируют плотность бетона, которую в натурных изделиях определяют по методике приложения 5; рассчитывают прочность на сжатие, призменную прочность и начальный модуль упругости бетона, а также его водо- и морозостойкость, для чего из каждого состава бетона изготовляют серию образцов, размеры которых и количество принимают согласно ГОСТам на каждый вид испытания. Примечание . В цилиндрическом сосуде емкостью 3...4 л последовательно приготовляют три замеса по 1,5...2 кг сухих каждый при установленном значении В/Т, отличающемся от расчетного на ±0,01; составляющие смеси взвешиваются с точностью до 1 г, перемешиваются вручную до однородного состояния и выдерживаются 3 мин; сосуд затем переворачивают и выдерживают в таком положении 20...25 с (смесь обладает достаточной текучестью, если на стенках сосуда остается не менее 2 и не более 7 % материалов, расходуемых на замес; если текучесть недостаточна, изменяют В/Т на 0,01 и повторяют опыт до получения удовлетворительных результатов; одновременно проводят опыт на смесях с первоначальными значениями В/Т при меньшем содержании регулятора гидратации; в случае большей текучести смеси в повторных опытах снижают величину В/Т или увеличивают содержание регулятора гидратации). Другой способ определения начальной текучести бетонной смеси и кинетики ее изменения во времени см. в приложении 4. Приемлемая для производственных целей бетонная смесь должна иметь достаточную текучесть в течение 12...15 мин с момента введения вяжущего. 4.12. Выдерживая требования п. 4.11, принимают рабочий состав бетонной смеси. Предпочтение следует отдавать смесям, содержащим минимальное количество дорогих и дефицитных материалов. 4.13 Предприятие-изготовитель должно располагать 2...3 составами бетонов, применение которых регламентируется свойствами сырья. Ячеистый конструктивный силикатный бетон на известковом вяжущем характеризуется относительно низким модулем упругости; для его повышения необходимо часть валовой извести (10...40 %) заменить клинкерным цементом, доля которого, вводимая в смесь, зависит от требований, предъявляемых к изделиям, и уточняется экспериментально. 5. ПОДГОТОВКА ФОРМ И АРМИРОВАНИЕ ИЗДЕЛИЙ 5.1. Изготовление изделий производится в металлических формах с откидными бортами, требования к которым регламентируются ГОСТ 18886-73*. 5.2. В процессе эксплуатации металлические формы необходимо подвергать периодическому осмотру для определения их технического состояния. Формы, внутренние размеры которых не отвечают нормируемым допускам, из технологического потока следует изъять. 5.3. Перед очередным бетонированием поддон и борта форм очищают от грязи, пыли и затвердевшего бетона. После очистки формы собирают и на внутренние поверхности наносят слой смазки толщиной 0,2...0,3 мм, которая не должна содержать примесей, оставляющих пятна на изделиях. 5.4. Укладку арматуры, предварительно покрытой защитной обмазкой ( приложение 2), выполняют после окончания подготовки форм. Арматурные сетки и каркасы укладывают в формы с расчетом, чтобы защитный слой бетона был не менее 20 мм. Сетки и каркасы в целях исключения возможности смещения арматуры из проектного положения при вспучивании бетонной смеси при укладке в форме закрепляются фиксаторами. 6. ПРИГОТОВЛЕНИЕ БЕТОННОЙ СМЕСИ И ФОРМОВАНИЕ ИЗДЕЛИЙ 6.1. Перед изготовлением изделий необходимо определить состав бетонной смеси, вид и оптимальное содержание регулятора гидратации в зависимости от свойств исходного сырья. 6.2. Составляющие бетонной смеси дозируются по массе. Песчаный шлам и воду допускается дозировать по объему. 6.3. В производственных условиях бетонная смесь должна сохранять текучесть 12...15 мин. На текучесть смеси и кинетику ее изменения во времени существенное влияние оказывают температура и скорость гашения извести, температура исходных сырьевых материалов (особенно воды, песчаного шлама и вяжущего). 6.4. Текучесть бетонной смеси регулируют корректировкой содержания и вида используемых регуляторов гидратации. В летний период следует применять воду с температурой 12...17°C, а вяжущие и шлам выдерживать после приготовления в течение 16...24 ч. В зимний период воду необходимо подогревать до 40...60°С с использованием свежеприготовленных шлама и вяжущего. 6.5. При использовании известково-цементного вяжущего целесообразно приготовлять бетонные смеси без регулятора гидратации. 6.6. При подборе и дозировании регуляторов схватывания и твердения необходимо учитывать, что смеси для изделий из ячеистых бетонов, приготовленные при низких значениях В/Т, обладают высокой начальной вязкостью, затем повышающейся за счет гидратации. 6.7. В процессе приготовление бетонной смеси газобетономешалка должна работать в таком режиме: запуск; введение в резервуар рассчитанных на один замес воды, песчаного шлама, регулятора гидратации и их перемешивание в течение 30...40 с; добавление карьерного песка и перемешивание смеси 2...3 мин; введение вяжущего и перемешивание смеси 3 мин; введение газообразователя и перемешивание 1 мин; разливка смеси в формы. Во избежание смывания смазки с поддона формы под струю смеси целесообразно подложить коврик. 6.8. На 0,75...0,9 часть высоты форма заполняется смесью за один прием. "Горбушка" должна быть не более 5 % объема формуемого изделия. 6.9. В случае применения известкового вяжущего один замес газобетономешалки должен обеспечивать формование изделий объемом не более 2 м3, известково-цементного вяжущего - соответственно 2,5...4 м3. 6.10. Изделия из ячеистого бетона формуют в закрытых помещениях при температуре окружающего воздуха не ниже 15 °С. Сквозняки не допускаются. Отделение формовки рекомендуется оборудовать подогреваемым полом. 6.11. Формы выставляются на горизонтальном полу с опиранием по всей плоскости. Перемещение форм до окончания процесса "созревания" бетона не допускается. 7. ПОДГОТОВКА ИЗДЕЛИЙ К ЗАПАРИВАНИЮ. ТЕПЛОВЛАЖНОСТНАЯ ОБРАБОТКА 7.1. Подрезку "горбушки" производят через 30...40 мин после завершения процесса вспучивания. "Созревание" бетона считается закончившимся после снижения температуры в глубине изделия на 10...15°. При этом бетон не должен прилипать к сухим пальцам оператора при легком нажатии. 7.2. "Горбушку" с открытой поверхности изделий необходимо удалять перед их загрузкой в автоклав. В изделиях, устанавливаемых на верхний ряд, удаление "горбушки" не обязательно (открытая поверхность защищена от воздействия конденсата). 7.3. Для повышения трещиностойкости бетона в сырых изделиях рекомендуется пробивать вертикальные отверстия диаметром от 6 до 8 мм на 2/3 глубины изделия по схеме, приведенной на рисунке. Схема расположения отверстий, на открытой поверхности стенового блока 7.4. Транспортирование сырых изделий и установку их на автоклавные вагонетки производят мостовым краном, оборудованным специальными траверсами, конструкция которых исключает деформирование продольных бортов форм. 7.5. Перемещение форм должно наполняться плавно, без толчков, поэтому рельсы следует тщательно подгонять, а рельсовые пути отрихтовывать. Перед началом производства работ необходимо проверить тормозные устройства кранов и устранить неисправности. 7.6. Ориентировочные режимы запаривания, ч : Подъем давления …………………………….2...3 (3...4) Изотермическая выдержка .…………………8...9 (6...8) Сброс давления ………………………………3…4 (3...5) Вакуумирование ……………………………….1 (1) Примечание. Режим запаривания приведен для максимального давления 8 ати (12 ати). Окончательно режим уточняется в процессе освоения производства. 7.7. После окончания процесса вакуумирования открывают крышку автоклава и охлаждают изделия до тех пор, пока разница между температурой в автоклаве и цехе составит не более 40°. 8. РАСПАЛУБКА, ХРАНЕНИЕ И ТРАНСПОРТИРОВКА ИЗДЕЛИЙ 8.1. Изделия до их распалубливания рекомендуется выдерживать в цехе в течение 2 ч при температуре не ниже 15 °С. 8.2. В процессе распалубки сотрудники отдела технического контроля (ОТК) предприятия производят осмотр, приемку и маркировку готовой продукции. 8.3. Готовые изделия должны храниться в закрытых складских помещениях в рабочем положении. Перемычечные блоки укладываются на деревянные прокладки штабелями высотой до 2 и длиной до 25 м. Между штабелями предусматриваются проходы шириной не менее 0,7 м. 8.4. Изделия поднимают и перевозят в положении, предусмотренном проектом. 9. КОНТРОЛЬ ПРОИЗВОДСТВА И ПРАВИЛА ПРИЕМКИ ГОТОВЫХ ИЗДЕЛИЙ 9.1. Лаборатория предприятия обязана производить контроль и анализ качества поступающих материалов, а также ведения технологического процесса. ОТК производит приемку готовой продукции, анализирует причины брака. 9.2. При поступлении на предприятие сырья контролируют: по содержанию активных CaO + MgO, температуре и скорости гашения, содержанию пережога и степени гидратации - известь; по марке, виду, началу и концу схватывания - цемент; по гранулометрическому составу, содержанию илистых, глинистых, органических примесей и гравия - песок кварцевый (не реже четырех раз в месяц); по тонкости помола - гипс полуводный; по марке - алюминиевую пудру. 9.3. Во время контроля производственного процесса проверяют: известь (известковое вяжущее) - по содержанию активных СаО + MgO (3...4 раза в смену), температуре и скорости гашения (1...2 раза в смену), содержанию пережога и степени предварительной гидратации (один раз в смену) согласно ГОСТ 22688-77; кварцевый песок - по содержанию влаги (3...4 раза в смену); песчаный шлам - по плотности и дисперсности песка (в процессе его приготовления и после заполнения шлам-бассейна); полуводный гипс - по тонкости помола (не реже одного раза в смену); суспензию алюминиевой пудры - в процессе ее приготовления; текучесть ячеистобетонной смеси (каждый 5...8-й замес); температуру ячеистобетонной смеси после выхода из газобетономешалки (каждый 5...8-й замес); длительность "созревания" бетона и температуру его разогрева (каждую 5...10-ю форму); плотность смеси (из каждой пятой формы); состояние весовых дозаторов (постоянно); режим запаривания (постоянно); состояние парка форм (1...2 раза в месяц); обмазку форм, качество арматурных сеток и каркасов (постоянно); приготовление защитных антикоррозионных покрытий арматуры и качество их нанесения на арматуру (постоянно). При изменении качества поступающих на предприятие сырьевых материалов лаборатория обязана вносить коррективы в технологический процесс. 9.4. ОТК предприятия контролирует: состояние и качество смазки форм, поступающих на посты формования (постоянно); качество арматурных сеток и каркасов, состояние защитных антикоррозионных покрытий, а также установку арматуры в формы (постоянно); плотность, влажность и прочность на сжатие бетона контрольных образцов (каждая партия изделий); размеры и внешний вид изделий - наличие трещин, сколов и других дефектов (каждое изделие). 9.5. Водо- и морозостойкость бетона устанавливают при организации производства и изменении источника снабжения сырьем. Текущий контроль производится не реже одного раза в квартал. 9.6. Натурные изделия подвергаются испытаниям до разрушения при организации их производства, текущие испытания - не реже одного раза в квартал. Испытания до разрушения производятся в соответствии с ГОСТ 8829-85. Испытанию подвергают не менее двух однотипных изделий. 9.7. Изделия принимаются партиями, каждая из которых состоит из изделий, изготовленных на одной смене и запаренных в одном автоклаве. Партия считается принятой, если показатели, качества изделий удовлетворяют требованиям действующих ГОСТов или ТУ. 9.8. На боковые грани принятых ОТК предприятия изделий несмываемой краской наносится штамп-марка с указанием: завода-изготовителя; даты изготовления; марки (типа) изделия; класса (марки) бетона; массы изделия; номера паспорта; штампа контрольного мастера. Наличие заводской марки свидетельствует о том, что изделие разрешено к отгрузке и монтажу. 9.9. На каждую партию изделий составляется паспорт, в котором указываются: наименование и адрес завода-изготовителя; номер; наименование изделий по ГОСТу или ТУ и их условное обозначение (индекс); номер ГОСТа или ТУ; количество изделий в партии; дата изготовления и приемки изделий; штамп контрольного мастера; класс (марка) бетона; плотность бетона; объем бетона и масса каждого изделия в отдельности; водопоглощение и морозостойкость бетона. 9.10. Администрация завода-изготовителя несет ответственность за качество отгружаемых изделий. 10. ОХРАНА ТРУДА, ТЕХНИКА БЕЗОПАСНОСТИ И ПРОТИВОПОЖАРНЫЕ МЕРОПРИЯТИЯ 10.1. При производстве изделий из ячеистых бетонов необходимо соблюдать следующие требования: не допускается курение в помещении формования изделий; в процессе работ по защите арматуры от коррозии составами, содержащими органические растворители, необходимо пользоваться специальной одеждой (комбинезоны, резиновые фартуки, перчатки, сапоги, респираторы, защитные очки). Помещения, в которых производится этот вид работ, должны быть оборудованы принудительной вентиляцией; на местах производства работ с органическими растворителями следует организовать противопожарный надзор. Эти места должны быть оснащены противопожарным оборудованием (огнетушители, кошма, ящики с песком и др.); вблизи емкостей с составами, содержащими органические растворители, во избежание взрыва недопустимы открытые источники огня; в местах нанесения защитных обмазок запрещается курение, пользование открытым огнем и выполнение работ, предполагающих искрообразование; органические растворители, краски и мастики на их основе следует транспортировать в герметически закрытой металлической таре в соответствии с Правилами перевозки огнеопасных продуктов. 10.2. Обслуживающий персонал должен быть ознакомлен с Правилами техники безопасности, производственной санитарии и противопожарной безопасности. Приложение 1 Рекомендуемое ОПРЕДЕЛЕНИЕ ОБЪЕМА ШЛАМА, РАСХОДУЕМОГО НА ИЗГОТОВЛЕНИЕ 1 м3 БЕТОНА Содержание воды, л (молотого песка, кг), в 1 м3 песчаного шлама в зависимости от плотности, кг/м3: В отличие от определения плотности пенобетонной смеси мерной кружкой плотность газобетонной смеси определяют металлической трубкой. Метод заключается в том, что после схватывания газобетона до срезки "горбушки" с помощью металлической трубки (рисунок) из изделия берут керн, для чего легким нажатием руки вдавливают трубку до дна формы и линейкой замеряют высоту верхней части трубки, не погруженной в ячеистый силикатный бетон. После этого вынимают трубку, предварительно закрыв ее резиновой пробкой или металлической крышкой (для удержания ячеистого бетона при ее извлечении из изделия). Схема трубки для отбора пробы вспучившегося ячеистого бетона 1 - металлическая трубка; 2 - резиновая пробка Образовавшиеся после взятия керна углубления заливают из очередного замеса раствором с газообразователем и дают возможность смеси вспучиться. Трубку с ячеистым бетоном взвешивают с точностью до 1 г по разности масс (трубка с бетоном и без него) определяют массу ячеистого бетона. По разности длин трубки и части ее, не вошедшей в бетон, определяют длину керна из ячеистого бетона и, зная внутренний диаметр трубки, вычисляют объем ячеистого бетона, а по объему и массе - его плотность в сыром состоянии. Зная плотность свежеизготовленного ячеистого силикатного бетона, В/Т и коэффициент, учитывающий увеличение массы сухого вещества в результате твердения за счет связанной воды Рс, можем подсчитать плотность ячеистого бетона в сухом состоянии: